Author | Topic |
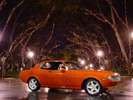
Toymods Board Member I supported Toymods
Location: Turramurra, Sydney.
Registered: May 2002
|
Re: Looking for .. Quick Shifter for Celica 5 speed
|
Tue, 08 October 2002 14:43
|
 |
There's a better article that goes into a bit more detail. Actually, I'll just put it up here for the time being. The pics link to the pics from the above (my) web page.
HEY NARK, I've done a bit of editing, so maybe you could use this post for the article (bar these first 2 paragraphs of course).
This is how I made (or had made really) a quickshifter for my T50 RWD sprinter 'box. Most RWD 'boxes would have a similar stick setup, and the same principal applies to all shifters.
First I guess I'll explain the basic principal of a quickshifter. The quickshifter's design and purpose is to shorten the length of the gear levers movement, while keeping the gearknob at pretty much the same height as before, meaning you can change gears quicker, because each gear position is closer. The reason you want to keep the stick at the standard height is to keep it close to the wheel, so your hand spends less time on it's way to the gear knob and off the sttering wheel changing gears, otherwise you're gonna be taking longer to reach for the gearknob..
So there's 2 ways to shorten the throw of the gear lever, you can cut the top part of the stick shorter, resulting in it beign further from the steeiring wheel, or you can make the bottom part of the stick longer, and raising the stick by a small amount. Both ways are decreasing the leverage of the stick, so it may feel a little stiffer, but it will usually feel better stiff (hey, it does for me!)
To lengthen the bottom part of the stick, you need to cut a section of the bottom half of it off, and weld it back on with a piece of rod inbetween it & the rest of the stick. Mine was done with an ARC/stick welder using a stainless steel welding rod, and looks like this..
It's a bit hard to make out, as the welds are fairly wide. This is because each end being welded was filed (with a file ) to a bit of a point, so the weld goes to the centre of the stick. Looking at that pic from right to left you see the ball on the end of the stick, a nice smooth section of stick about 5mm, then about 10mm of shiny stainless steel weld, then a shortish rough section of rod, a bit darker than the rest, then another 10mm or so of weld.
The section of rod is actually about 20mm long, but is covered by the weld. If you can imagine 2 pointy sticks with their tips together, and the weld filling up around the tips to make it fairly round again (like in the pic). it's actually 2 pointy sticks with a really short double pointy ended stick inbetween. If you wanted, you could grind it all down a bit to make it smooth, but I felt it unnecessary.
Ok, as you can see in the next pic, the length was increased to 50mm, which is a total increase of almost 70% over the original 30mm.
Now the next bit you need is a plate to raise the pivot point of the shifter. Seeing as you just made the stick longer, the base plate that holds the stick and bolts down to the gearbox will now sit (in my case) 20mm higher than it used to, making it a bit tricky to bolt in. Find yourself a piece of alloy that is the same thickness or thicker than you've lengthened the stick. If it's thicker, you can just have it milled down to the exact thickness. Actually if you can start with a piece the exact thickness you will need, you would be able to make it with a hacksaw, a file and a drill (although your arm would be tired). I initially planned to use numerous 3 or 4mm thick plates, as it was easier to get hold of (I was doing this on a budget of nothing, and over a long time while my car was off the road), but the piece I ended up getting my hands on was actually about 60mm thick. I was told the milling machine made short work of it.
So use your base plate or baseplate gasket as a template, and cut the alloy plate to the right shape. A bandsaw comes in handy for this. Next drill four centre holes so you can cut out the centre section of the raise plate. You don't need to make this hole as big as the actual hole, you'll see what I mean when you pull out your shifter. Finally, drill the four bolt holes.
It should look a bit like the one in this picture (the shiny thing on the right, with the base plate to the left of it & 2 gaskets below it):
The only other bits you need are in this pic, and that's some longer bolts and 2 new gaskets. The gaskets can just be cut out of gasket paper, which will cost you 5-10 bucks for enough paper to make plenty of gaskets, and the bolts shouldn't be too hard to find. I got mine from a nearby parts store.
Assembly is pretty basic, put a gasket either side of the raise plate, and bolt it all back into place.
The last step is to take your car out for a drive, & marvel at the wonderfully short shift! It will take some getting used to, and you may find yourself shifting from 2nd to 5th every now & then, but once you get used to it, you'll wonder how you ever did without it.
Thanks go to Erick McVicker, whom I used to work with, for doing the welding, and Noel Richard for helping me out with the raise plate.
BTW, Erick made an interesting/worrying point. He reckons the end of the stick that's being cut & welded would be hardened, and cutting and welding it would take away its hard properties, which could lead to fatigue stress. Everyone I've talked to that have done similar quickshifters have never had problems with this, and mine has been fine for quite a while now, but it is something to consider.
Now that I think about it, grinding it back smooth & and giving it a bit of a polish would reduce the chances of cracking, but I'll leave it up to you.
[Updated on: Tue, 08 October 2002 15:27]
|
|
|
Current Time:
Mon Jul 21 01:21:01 UTC 2025 |
Total time taken to generate the page: 0.0062780380249023 seconds |