Author | Topic |
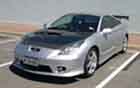
Location: Adelaide
Registered: May 2002
|
Re: 2ZZGE Conversion to RWD
|
Tue, 28 May 2002 16:50

|
 |
Current 2ZZ-GE in the front wheel drive Celica is mated to the C60 close ratio 6 speed gearbox. This package (engine/gearbox)is also used in the Toyota Matrix in USA, which is a 4WD vehicle (very similar type of car to the Honda CRV).
I've read on club4ag, a AE86 had a F20C engine conversion. But thats from a Honda S2000 which is a rear wheel drive setup in the first place already.
t, I've heard of mis-shifting the gearbox ocurring in the US (eg downshifting from 5th to 3rd but accidently put into first to blow the engine). But hav'nt heard many cases of burnt vavles. Are the valves that weak? where to you work or get the info from? Very interesting
Info on the 2ZZ-GE (copy and pasted)
Toyota's all-new Celica engine has state-of-the-art production-engine features. The Yamaha-built 1.8 litre engine has 40 percent more power than the 2.2 litre engine it supersedes in the previous Celica. It has the highest specific power output of any naturally aspirated engine in the Toyota range. The 1796cm3 Celica engine delivers 140kW of power at 7600rpm and 180Nm of torque at 6800rpm. The intelligent Toyota system (VVTL-i) offers infinitely variable inlet timing across the revolution range and provides high-lift for both camshafts when engine revolutions exceed 6000rpm. Toyota has adopted leading-edge engine technology throughout the new Celica engine, for maximum fuel efficiency, low emissions, light weight, low NVH and high performance. Features of the Celica 2ZZ-GE engine include: * a compact, externally ribbed all-alloy cylinder block with metal matrix composite (MMC) material cylinder walls to achieve linerless construction. The alloy block delivers maximum thermal efficiency and minimum weight. * passage holes in the crankshaft bearing area of the block, to reduce pumping losses within the engine and hence boost performance * a water-pump swirl chamber and the inlet passage to the pump integrated into the block, to save weight, space and complexity * a full ladder-type crankshaft bearing cap, to maximise rigidity and reliability, and reduce noise. The full-ladder bearing cap also improves the coupling to the transaxle. * a bearing cap with chill-fitted cast-iron inserts around the journal portions, to resist heat deformation. * the oil-filter bracket, air conditioner compressor bracket and rear oil-seal retainer are integrated into the bearing cap to reduce the number of parts * serpentine belt drive to the auxiliary equipment, to reduce engine length, number of parts and weight * a fully balanced crankshaft and thin, lightweight, high-strength connecting rods to reduce reciprocating weight and friction * a square bore and stroke relationship to boost torque (82.0mm x 85.0mm) * flat-topped pistons with valve clearance cut-outs to achieve an 11.5:1 compression ratio. The pistons are iron and tin-coated to reduce friction.
Cylinder Head Design:
Toyota Celica has an all-alloy Twin Cam Multi-valve cylinder head. The valve seats are made by welding high-resistance material into the port, then machining a valve seat into the material. The resulting valve seat can be made thinner than a conventional shrink-fit valve seat, for improved air flow and better cooling around the valve area. The camshaft drive is by 8mm pitch roller chain, with a lubricating oil jet and auto tensioner. The Celica engine has long straight intake ports, to further boost engine breathing. It has narrow valve stems, to reduce intake resistance and valve-train mass. The fuel injection nozzles are located in the inlet ports, to prevent wall wetting and fuel adhesion to the walls of the port, thereby reducing hydrocarbon emissions. Celica's compression ratio has been set at 11.5:1, for optimum combustion efficiency and power output across the revolution range. The combustion chambers have a tapered squish design, to improve thermal efficiency and reduce the chance of engine knock (pre-ignition). The squish angle has been shaped obliquely along the wall surface of the combustion chamber, to improve airflow, promote swirl and speed flame travel. Further features of the Celica engine's top end are: * an aluminium intake manifold with a die-cast aluminium air chamber and a resonator to optimise mid-range torque. The intake duct has a variable valve, which is closed at low engine revolutions to reduce noise. * sequential electronic fuel injection with four-hole injector nozzles mounted in the inlet ports, for maximum fuel atomisation and reduced wall wetting * an L-type hot-wire air flow meter for the EFI, for more accurate air-flow measurement and hence more accurate fuel/air mixing * a four-into-two-into-one extractor-type exhaust system (using a metal separator plate in the exhaust union), to boost torque * double-walled front exhaust pipe, for maximum performance and durability, and lower emissions * rearward-facing exhaust, which combines with the double-walled front pipe to improve catalytic converter performance and hence reduce emissions. The catalytic converter has thinner walls to further improve heat-up rate. * a cross-flow type aluminium radiator for improved cooling, increased recyclability and reduced weight. Service weight of the Celica engine has been reduced by nearly 25 percent compared with previous engine. Additional fuel and emission saving technology includes computer engine management, individual Toyota Direct Ignition for each of the four cylinders and electronic spark advance with a knock control system. Further serviceability improvements include Multiplex engine diagnostics (which can detect a malfunction and memorise the failed section). Toyota Celica also has a fuel cut-out device, which activates if the airbag SRS is deployed.
VVTi and Variable Lift:
Toyota Celica's state-of-the-art 1.8 litre 2ZZ-GE engine has intelligent variable valve timing and intelligent variable lift (VVTL-i). The variable valve timing and variable lift technology gives Celica a combination of driveability, fuel efficiency, low emissions and high performance. Toyota's intelligent infinitely variable valve timing system is more advanced than the binary systems in some German luxury vehicles and Japanese small cars. VVTi is a flow-down from the Lexus luxury car program and the Prius hybrid vehicle. Celica has the latest-generation TMC-developed vane-type VVTi control, which is used on Prius, Lexus IS200 and Echo. Intelligent variable valve timing will go into widespread use on Toyota vehicles. VVTi provides continual variations of the intake valve timing, to provide ideal valve timing (and hence ideal engine characteristics) for the full range of driving conditions. High Lift, Long Duration: Toyota's variable valve lift system operates on the inlet and exhaust valves. The Toyota 2ZZ-GE engine switches to the high-lift camshaft settings at 6000rpm. The high-lift cam lobes increase intake lift by 54 percent to 11.2 mm and exhaust lift by 38 percent to 10.0mm. The high-lift cam profiles have the effect of increasing valve-opening duration, and therefore the range of inlet timing variation. Valve overlap can vary between 4 degrees (full-retard inlet setting and low-speed lift settings) and 94 degrees (full advance inlet and high- speed lift settings). A valve overlap of 94 degrees would normally be associated with full race engines. For comparison, superseded Celica's 5S-FE engine had six degrees of valve overlap and the sports two-litre 3S-GE engine in the first front-drive Celica model had 14 degrees of overlap. Inlet camshaft timing is varied according to engine revolutions, throttle position, inlet camshaft angle, engine coolant temperature and intake air volume. Variable Timing Activation: Toyota Celica's VVTi is a computer controlled and oil-pressure activated push-push type system, using the engine oil. The engine ECU can command the system to advance or retard the inlet camshaft timing, thereby providing for faster response. The hardware is a camshaft timing oil control valve (mounted adjacent to the inlet camshaft gear wheel) and a VVTi controller mechanism built onto the inlet camshaft timing gear. The camshaft timing oil control valve is a spool valve, controlled via a coil and plunger by the engine ECU. It can signal advance, hold or retard. The VVTi controller consists of a housing on the front of the timing wheel, driven from the timing chain, and a four-bladed vane coupled with the intake camshaft. When the engine ECU requires a change in inlet timing, it signals the oil control valve to provide oil pressure to either the advance or retard side of the four vane chambers. Inlet cam timing is set to the maximum retard position for engine start-up, operation at low engine temperature, idle and engine shut-down. A locking pin in the controller locks the camshaft timing in the maximum retard position for engine start-up and immediately after start-up (until oil pressure is established) to prevent any knocking noise. Celica's VVTi system can vary inlet camshaft timing over a range of 43 degrees relative to crankshaft angle. However, the variable lift system has the effect of increasing valve opening duration, so the full range of inlet timing variation is 68 degrees. (Taken from the maximum retard intake valve opening in the low-medium engine speed range at minus 10 degrees BTDC to the maximum advance intake valve opening in high engine speed range at 58 degrees BTDC.)
Variable Lift Activation:
Toyota's intelligent variable valve lift system uses a cam change-over mechanism to increase the lift of the intake and exhaust valves when engine revolutions exceed 6000rpm. The hydraulically activated variable-lift mechanism is electronically controlled by the engine ECU and shares some of its hydraulic control hardware with the VVTi system. It has the same system inputs as the VVTi system - crankshaft angle and revolutions, air flow, throttle position, inlet camshaft angle and engine coolant temperature. The variable-lift system will not operate until coolant temperature reaches 60 degrees. The mechanism includes camshafts with two sets of cam profiles, for low-to-medium engine speed and high engine speed (high lift). The full system includes eight rocker arms (one for each pair of valves), two rocker shafts (located inboard of the camshafts) and a spool-type oil control valve on the aft end of the inlet camshaft. The rocker arms are the heart of system. They have an integrated needle roller cam follower, a rocker arm pad and hydraulic rocker arm pin. In normal operation, the low-to-medium speed cam acts on the needle-roller cam follower and the rocker arm operates its pair of valves. Meantime, the rocker arm pad rides against the high-lift cam lobes, but moves freely within the rocker arm. In this state, the rocker pad does not contribute to rocker arm movement and therefore makes no contribution to valve activation. When the engine is operating in the low-to-medium speed ranges, the oil control valve is open to the drain side. However, when engine revolutions exceed 6000rpm, the oil control valve closes the drain side and hydraulic pressure flows through the rocker shafts to the hydraulic rocker arm pin. The hydraulic pressure pushes the rocker arm pin out to lock the bottom of the rocker arm pad. With the rocker pad locked in its full extended position, the high-lift (high-speed) cam lobes now operate the rocker arm and hence its pair of valves. When engine revolutions drop below 6000rpm, the oil control valve opens on the drain side, to relieve pressure on the cam changeover mechanism and allow the system to return to normal lift conditions. Celica's 2ZZ-GE engine has shim-type valve clearance adjusters and narrow valve stems to optimise gas flow.
Transmission:
Toyota developed the new C60 six-speed manual transmission to increase driving enjoyment and provide a gear for every corner. The six-speed manual transmission is standard equipment in Celica. An electronically controlled four-speed automatic transmission with Formula One style E-shift is available as an option. The Toyota C60 manual transmission has close ratios from first to fifth gears, and a tall sixth gear for increased fuel economy and reduced noise on the highway. All forward gears in the C60 transmission are constant mesh, which use an inertia lock key type synchromesh mechanism. Particular attention has been paid to shift quality, with a crisp, short-throw lever and positive shift feel. The C60 transmission has double-cone synchromesh on the first-second change, to improve shift quality and gearbox durability. Shift feel has been further improved by adopting Teflon bushings on the support portion of the shift and selector shaft, a mass damper on the shift and selector shaft, and a rolling-type lock ball assembly. The shift pattern has fifth and sixth gears on the same longitudinal plane. Reverse gear is forward and away from the driver. A spring-loaded mis-shift function has been adopted to prevent mis-shifting into reverse gear when selecting either first or second gear from neutral. In addition, new Celica has a reverse shift warning buzzer, which sounds when the manual shift lever is shifted into reverse. The Toyota C60 transmission has ratios of: first, 3.166; second, 2.050; third, 1.481; fourth, 1.166; fifth, 0.916; sixth, 0.725 and reverse, 3.250. It is matched to a final drive ratio of 4.529:1. Celica's clutch has a diaphragm turnover mechanism for crisper clutch action. Clutch plate thickness has been increased by 11 percent compared with superseded Celica, to increase durability. The new 212mm diameter clutch has 199cm2 of facing area.
|
|
|
Current Time:
Sun Sep 7 04:23:55 UTC 2025 |
Total time taken to generate the page: 0.003154993057251 seconds |