Author | Topic |
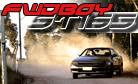
Location: South Australia
Registered: July 2002
|
Re: Rebuilding Bottom End - need some advice!
|
Thu, 29 September 2005 15:39

|
 |
Ahh some awesome responses - now for the hard part - replying to 'em 
o_man_ra23 | A rod bolt is possible as they use a nut on the end... but how far will the bolts stretch at the required torque?? this is a complex mathematical equation dependant on impurities in the material of the bolt, the heat of the bolts, and how much the head squashes on the con-rod (among other things)... so it is also innacurate. Personally i would just take my time to make sure those threads are perfect (mostly just for the main bearing threads in the block, because all your bolts and nuts will be new, and should have high precision threads).
| Yeah I think you are partly right, but I imagine that most rod bolt manufacturers (such as ARP) give info on how much stretch is required for the correct torque is because it's possible to 'calculate' how strong the material is, I haven't checked, but i'm sure instructions relating to lube, heat etc are also supplied with most new bolts.
Big T | do know what you're refering to here... it was on the ARP website tech docs but the site is down atm. Apparently it is THE most accurate way of bolting stuff down but i thought you needed VERY precise tools in order to measure it.
Just get some ARP moly lube and use that to torque to specs. Just make sure you tighten/loosen the bolts by hand 3-5 times to make sure the thread is properly coated.
| Yeah I imagine that the average micrometer is probably not going to be accurate enough, so I may have to look into finding a better tool for the job.
4agte | exactly its not like your building a formula 1 engine thats going to spin to 18k
| Actually I'm building a few 3S engines at the moment - one of which is going to go into a very serious track car So I'm trying to do the best I can and learn as much as possible in the process. Plus I know how much track engines (and even road engines when I'm driving) get thrashed so I'm trying to build them as *strong* and *reliable* as possible. I've rebuilt an engine or two before, and I've helped my dad build a couple of rally car motors, and it's seriously tough to get them right and build it as good or better than factory spec.
starfire | I would suggest that if you are serious about this rebuild pick up a book on the subject. You may find it hard to find one that specialises in the 3SGTE, but ones on the small block Chev (350) are usually pretty easy to find and cheap. The principals are all pretty much the same, but the tolerances will be different - Toyota would have reccomendations but if you are using aftermarket parts you will need to check their clearance specs too.
An added bonus of reading such a book is that you will gain a good understanding of the processes that are available to you from the machine shop.
That way when you walk in there you can ask for exactly what you want and are much more likely not to be ripped off or get something that is not to your required specifications.
Regards,
Terry.
| Yeah, books, tech articles, etc I'm currently reading and trying to absorb as much as possible, but also I realise that until I actually *do* some of this stuff it's all a waste of time 
jeffro RA28 | To measure stretch we use a stretch gauge. The rod bolts should have a dimple in either end. Picture an outside micrometer with a dial indicator. Or the oposite of a ball gauge. A torque wrench is used as a guide othersie u ill not know when to start measuring the stretch. The rod bolt manufacturer should supply you with a info sheet on doing this and also what they recomend the stretch to be.
To precisly meaure the oil clearance of your bearings you will need an outside micrometer and a ball gauge. The ACL bearing book or your engine manual should provide the correct oil clearance figure.
To measure oil clearance
1: Install bearings and caps and torque down.(always use lube on bolts, not only to get more accurate figures but to lube the bolt and help it from galling)
2: measure crank journals with a mic.
3: Put the ball gauge between the mic when it is set on the journal size. Then zero the dial on the ball gauge dial indicator.
4: Use the ball gauge inside the torqued bearing cap and bearings.
You should get a positive reading on the dial. If its negative u have lots of work to do.
Telescopic gauges are only as good as there user. the same with any precise measureing tool. They do take a little more skill and experience to use accurately tho.
these instruments are not your everyday worshop tool tho.
| So a stretch gauge is very similar to a dial guage, only a) more accurate, and b) has some way of settling in the dimple at the end of the rod bolt.
allencr | 1. pretty good site. look around http://chevyhiperformance.com/techarticles/49258/
2. Plastigage is the best thing since sliced bread except for microwave ovens & 4AGs. it does not tell if it is out-of round. i've only heard that the rod side play will skew it some, and that some will use a temporary shim to keep it from twisting when tightened. not my experience.
3. practice!! try Starrett, their site might have something. you can do it with a piece of coat hanger, with radiused & very smooth ends, and your mic/vernier caliper if you have to.
4. yes, the clearance is on the skirt, and except for the pin & ring land dimensions, most else would be usless.
5. indexing/degreeing the crank is nice, just to know its OK, but my stuff wasn't that precision and it only really matters in respect to cam & ignition timing being off compared to the one used to set them. TDC on 1 & 4 at zero, and 2 & 3 at 180.
You CANNOT do this with a factory pully, on any engine in the world!! its gotta be bigger to be accurate.
most cranks get bent/warped. use the #1 & #5 mains(with bearings& oil) as a V-block and use #3 main to check its runout. zero is nice. the Toyota FX16 book RM069U says .0024in max. a dial indicator isn't necessary, and just a stiff wire bolted to the pan rail & feeler gage can make a good indicator & measurment.
i just used the cap, #3, with 2 bearings & none in the block(except #1 & #5) tightened down slowley, bit by bit, to bend it straight. take it easy, a little bit more each time. steel springs back more then cast, i imagine. i've never done it on cast iron.
6. machining what??? valve relief, pin size, ring land width or depth, shortened skirt, extra oil ring/scraper? it's just a piece of metal and it isn't heat treated, though it may have a coating.
| part 1 thru 4 are all understood...but part 5 I'm assuming that in the case of a straight 4 (ie the 3S motor that i'm working on) you would put the caps on 1 & 4 and check the run-off on 2 & 3. I would also assume that the block is usually alot straighter than the crank, but is there any way of checking the block to make sure that you aren't bending the crank for nothing? Maybe using a very precise straight edge? Lastly - when you say use 2 bearings on #3 (in your V engine example) you mean 2 bearings in the #3 cap, and no bearing in the block?
And in regards to the piston machining I mean valve reliefs or circumference of the piston crown. I always thought that cast *anything* is not very crack resiliant when machined as the surface is where the material is stronger?
jeffro RA28 | Oh and when your measuring your piston clearance usually u measure at the centre height of the piston pin. With forgies u measure half an inch from the bottom of the skirt.
| Cheers for that.
|
|
|
| Subject | Poster | Date |
 |
Rebuilding Bottom End - need some advice!
|
RWDboy | Mon, 26 September 2005 10:59 |
 |
Re: Rebuilding Bottom End - need some advice!
|
gemtoy | Mon, 26 September 2005 11:48 |
 |
Re: Rebuilding Bottom End - need some advice!
|
RWDboy | Mon, 26 September 2005 13:20 |
 |
Re: Rebuilding Bottom End - need some advice!
|
RWDboy | Mon, 26 September 2005 13:26 |
 |
Re: Rebuilding Bottom End - need some advice!
|
BigBadBenny | Tue, 27 September 2005 12:17 |
 |
Re: Rebuilding Bottom End - need some advice!
|
RWDboy | Tue, 27 September 2005 13:02 |
 |
Re: Rebuilding Bottom End - need some advice!
|
wilbo666 | Tue, 27 September 2005 14:01 |
 |
Re: Rebuilding Bottom End - need some advice!
|
Big T | Wed, 28 September 2005 00:01 |
 |
Re: Rebuilding Bottom End - need some advice!
|
4agte | Wed, 28 September 2005 05:32 |
 |
Re: Rebuilding Bottom End - need some advice!
|
RWDboy | Tue, 27 September 2005 12:58 |
 |
Re: Rebuilding Bottom End - need some advice!
|
o_man_ra23 | Tue, 27 September 2005 23:26 |
 |
Re: Rebuilding Bottom End - need some advice!
|
Starfire | Wed, 28 September 2005 06:12 |
 |
Re: Rebuilding Bottom End - need some advice!
|
jeffro RA28 | Wed, 28 September 2005 06:53 |
 |
Re: Rebuilding Bottom End - need some advice!
|
kingmick | Wed, 28 September 2005 21:01 |
 |
Re: Rebuilding Bottom End - need some advice!
|
allencr | Wed, 28 September 2005 14:53 |
 |
Re: Rebuilding Bottom End - need some advice!
|
jeffro RA28 | Wed, 28 September 2005 22:48 |
 |
Re: Rebuilding Bottom End - need some advice!
|
kingmick | Wed, 28 September 2005 23:51 |
 |
Re: Rebuilding Bottom End - need some advice!
|
jeffro RA28 | Thu, 29 September 2005 01:38 |
 |
Re: Rebuilding Bottom End - need some advice!
|
RWDboy | Thu, 29 September 2005 15:39 |
 |
Re: Rebuilding Bottom End - need some advice!
|
jeffro RA28 | Fri, 30 September 2005 02:06 |
 |
Re: Rebuilding Bottom End - need some advice!
|
RWDboy | Fri, 30 September 2005 12:54 |
 |
Re: Rebuilding Bottom End - need some advice!
|
allencr | Sat, 01 October 2005 03:57 |
 |
Re: Rebuilding Bottom End - need some advice!
|
RWDboy | Sat, 01 October 2005 04:49 |
 |
Re: Rebuilding Bottom End - need some advice!
|
allencr | Sun, 02 October 2005 12:32 |
 |
Re: Rebuilding Bottom End - need some advice!
|
RWDboy | Mon, 03 October 2005 06:10 |
 |
Re: Rebuilding Bottom End - need some advice!
|
kingmick | Mon, 03 October 2005 07:09 |
Current Time:
Fri Aug 1 22:49:28 UTC 2025 |
Total time taken to generate the page: 0.0034420490264893 seconds |