Author | Topic |
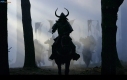
Location: Ballarat
Registered: September 2003
|
2tg sump modification
|
Sat, 23 October 2004 10:02
|
 |
hey ive heard that the 2tg dry sump setup isnt ideal...and that it will benefit from a baffled setup.
um, can someone explain the difference between the systems? and the pros/cons if possible
cheers
|
|
|
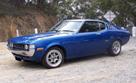
Location: Terrigal
Registered: May 2002
|
Re: 2tg sump modification
|
Sat, 23 October 2004 10:41

|
 |
I'd try talking to YelloRolla about this one, he has setup quite a few sumps and knows his stuff.
Cheers
Joel
|
|
|
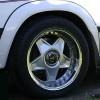
Location: Brisbane
Registered: May 2002
|
|
|
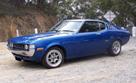
Location: Terrigal
Registered: May 2002
|
|
|
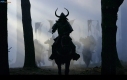
Location: Ballarat
Registered: September 2003
|
Re: 2tg sump modification
|
Sat, 23 October 2004 10:55

|
 |
yeah, i dont know anything about the two at all. i think i got dry sump for a 2tg coz i looked at the specs for the rallt version of the ta22.
just a quick q, obviously i will need a proper rundown, but what sort of thing would u do as a baffling procedure?
|
|
|
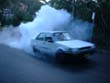
Location: Hornsby, N.S.W
Registered: September 2002
|
Re: 2tg sump modification
|
Sat, 23 October 2004 11:01

|
 |
you would weld small walls into the sump to help reduce oil splash and sway!
|
|
|
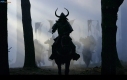
Location: Ballarat
Registered: September 2003
|
Re: 2tg sump modification
|
Sat, 23 October 2004 11:10

|
 |
hey juzzo sign into msn if you can, gotta have a quick chat to you about the cam specs (again)
|
|
|
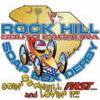
Location: Adelaide, Semaphore
Registered: September 2004
|
Re: 2tg sump modification
|
Wed, 24 November 2004 22:27
|
 |
Hiya Untouchable....
Did you find out the info on baffled sump verses dry sump?
I have done baffles in most engines that I rebuild for club events, It is very easy if you have a bit of time. Done properly, you will have very little problem on oil starvation on hard cornering. Don't just cut steel and just weld in wherever. While the engine is completely stripped cut min. 1.5mm sleel zintex to the shape of your cardboard templates of the sump. Make sure you have your crank and oil pump/pickup still in the block, so as to fit the templates in such possition as to miss the moving parts and pickup. Make sure you cut the zintex 5mm bigger than your template so you can cut tabs into the profile and bend at 90 deg. Once you mark out where the templates fit best, get a small dremel or di-grinder to clean up the area you will be brazing to. I find that brazing works best in this small job as it has a little bit of flex in the weld. The secret here is to make sure that for every inch of steel you have on the baffle plate there is an 8-10mm hole drilled and deburred. The importance of these holes is that you will still have constant flow. The trick is to make sure the holes start at the base of the plates so that you will have flow at the bottom of the sump. Carefully line up your plates into the sump with the marks you have made from the templates and tack into place on each corner. Once all plates are in place, place the sump onto the block and recheck for any interferance. At this stage, all should be ok. Its now time to stitch braze into place and then finaly clean up any small bits of suspect braze. The last thing you want is to have a bit of weld come loose in your block.
|
|
|