Author | Topic |
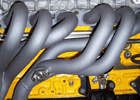
Location: Lost in the K hole
Registered: May 2002
|
|
|
Location: Cairns
Registered: May 2002
|
Re: welding stuff to a cast exhuast manifold ??
|
Wed, 30 October 2002 05:44

|
 |
I have welded cast with stick welder and WIA cast iron rods. PITA. Can be done, but you REALLY have to want it.
JIMMYD
|
|
|
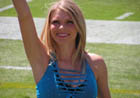
I supported Toymods
Location: I renounced punctuation
Registered: May 2002
|
Re: welding stuff to a cast exhuast manifold ??
|
Wed, 30 October 2002 06:11

|
 |
Apparently the cast needs to be heated to a cherry red color, then welded, and then allowed to cool. Apparently there are probs with the welds just cracking. It can be done but is a major PITA.
Read here for a summary of the problems. These guys are selling a special cast rod and presenting it as if it were a magical cure-all.
Brazing might be another way around the problem.
|
|
|
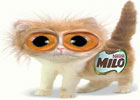
Location: Bundaberg, Qld.
Registered: May 2002
|
Re: welding stuff to a cast exhuast manifold ??
|
Wed, 30 October 2002 12:20

|
 |
when i modified my cast manifold, i got the turbo flange 'brazed' on, that shit is tough, works heap better and easier than welding, also did it with the dump pipe....
all the searching i did on the web, recommened 'brazing' cast...
|
|
|
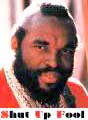
Location: Canberra
Registered: May 2002
|
Re: welding stuff to a cast exhuast manifold ??
|
Wed, 30 October 2002 12:28

|
 |
A mechanic mate of mine has modified several cast dump pipes and turbo exhaust flanges off nissan RB series motors, they seem to have high quality metal in their castings, and have had no problems after a few years of use.
He heats them up with an oxy first, then welds with high current on a MIG, to get good penetration.
dunno about the quality of toyota cast parts.
|
|
|
Location: Finland
Registered: June 2002
|
Re: welding stuff to a cast exhuast manifold ??
|
Wed, 30 October 2002 21:46
|
 |
This one professional welder told me that heat treatment _after_ welding does the trick.
He for example welded up this one truck exh header. He used stick weld, some kinda 'chrome'-stick.
Anyways, wlded the crack up, installed header, and used engine itself to do the heat treatment.
Switched engine on for 1 to 2 minutes, had it idling all time. Swicth off, cooling period. After a while, switch back to idle, leave it running longer, cool down again.
Work this way carefully towards normal temperatures.
Apparently if it has inbuilt stresses inside wlding, it'll crack during first time it's running. If it'll make trhrough one day, it won't (most likely) crack at weld seam.
He said that sometimes on construction sites they ne really long drill bits. Those are done on site. Just weld on a rod onto a drill bit. He said it's cruicial to use blow torch to after welding to heat it until dark red - then have it cool down slowly.
If after treatment not done - drill bit will eventually crack away from metal rod.
-A.
|
|
|